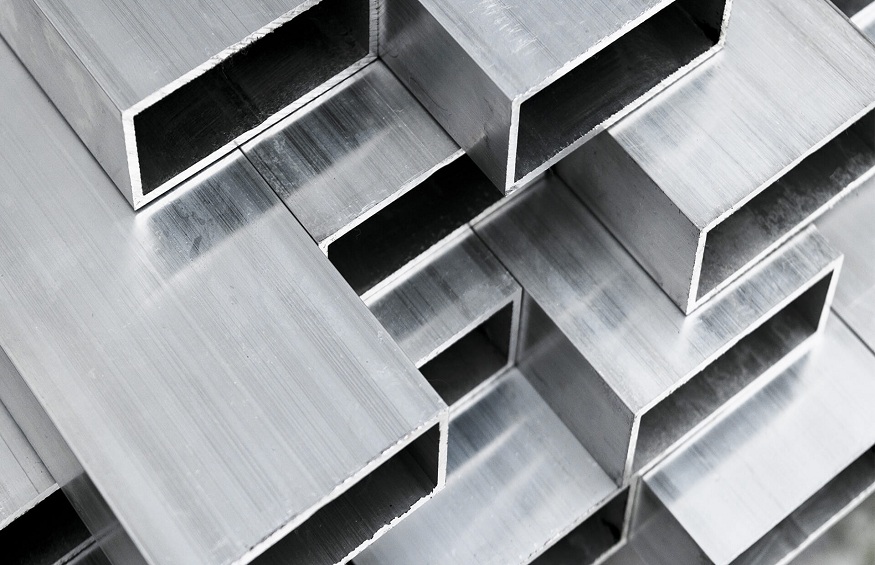
When considering using aluminum extrusion, it’s essential to know the process. It’s also essential to understand the process’s limitations so that you can choose a company that can produce high-quality products. Fortunately, there are some basic rules of thumb to ensure your extrusion projects turn out as smoothly as possible.
Hot Extrusion vs. Cold Extrusion
You can choose either hot or cold extrusion depending on the material used. Each method has its advantages and disadvantages. Nevertheless, both have a wide range of applications.
Using cold extrusion, you can get a better surface finish than you can with hot extrusion. Also, cold extrusion has better strength. Cold extrusion is also more cost-effective. Typically, cold extrusion is used with metals that can withstand extrusion stresses, such as titanium, copper, and lead.
The process of hot extrusion is similar to cold extrusion. The only difference is that hot extrusion involves lubrication. Lubrication is used to protect the die surfaces and minimize friction. Lubricants can be made of oil, graphite, or other materials.
While cold extrusion is used for a wide variety of materials, it is most commonly used with aluminum. In addition to being lightweight, aluminum has good thermal conductivity and corrosion resistance. This allows it to be used in many applications.
Characteristics of extruded aluminum
Various extrusion processes have been developed for processing aluminum alloys. Aluminum is characterized by its high strength-to-weight ratio, excellent resistance to corrosion, and ability to rebound from impact. These features make aluminum suitable for a variety of applications.
Aluminum extrusions Toronto is an ideal material for many building applications. It is light, durable, and environmentally friendly. It can be shaped to meet specific structural needs and has a wide range of finishes. Using extruded aluminum in commercial projects can increase the longevity of a building.
Extruded aluminum is also used for transportation and electrical and magnetic applications. It is a good choice for multifamily projects because it is a sustainable material. In addition to its benefits, extruded aluminum is a green building material.
Extruded aluminum is characterized by its high surface quality. Depending on the quality of the workpiece and the pressing technology, the surface of extruded aluminum will be smooth and clean. Its surface also has excellent corrosion resistance.
Anodizing
Adding a protective layer to aluminum extrusions increases the longevity and durability of the aluminum. This makes it ideal for industrial, commercial, and consumer applications.
The anodizing process takes advantage of a natural reaction that occurs on aluminum. The resulting artificial oxide film is solid and resistant to corrosion, abrasive cleaners, and sunlight. The anodic coating has a porous structure that allows for secondary infusions of dyes and other additives.
During the anodizing process, an electric current passes through a solution of metal salts, such as copper, zinc, nickel, and aluminum. The resulting electrolyte fluid contains oxygen ions, which attract to the aluminum. The chemical reaction creates an oxide layer thicker than the naturally occurring layer.
Anodizing aluminum extrusions also provide light, corrosion-resistant components for various applications. The finish is durable, easy to clean, and easy to maintain.
Aluminum anodizing is also available in a variety of colors. Some colors are bright, while others are a matte finish. Manufacturers often add dyes to the solution to add color to anodized aluminum. These dyes fill the pores throughout the thickness of the oxide layer, creating a colorful effect.
Quenching
During quenching, the workpiece is heated to a high temperature, then quickly cooled to a lower temperature. The goal of this process is to increase the strength and rigidity of aluminum components. To achieve this goal, different quenching techniques are used.
Water cooling is a popular technique for quenching aluminum alloys. Because water is readily available and inexpensive, it can be used to achieve rapid quenching speeds.
Air cooling is also used. The process is not as uniform as water cooling but results in a more rapid quenching.
Spray quenching is also used for aluminum heat treatment. This method requires a careful study of the process. The spray quenching method must be appropriately used to achieve the desired properties. The shape, size, and alloy must be correct. The quench sensitivity and thickness must also be investigated. The process should be verified by cooling curves in the production chamber.
The process of quenching aluminum alloys has its challenges. The process must be fast enough to avoid undesirable behavior, such as a decrease in strength.