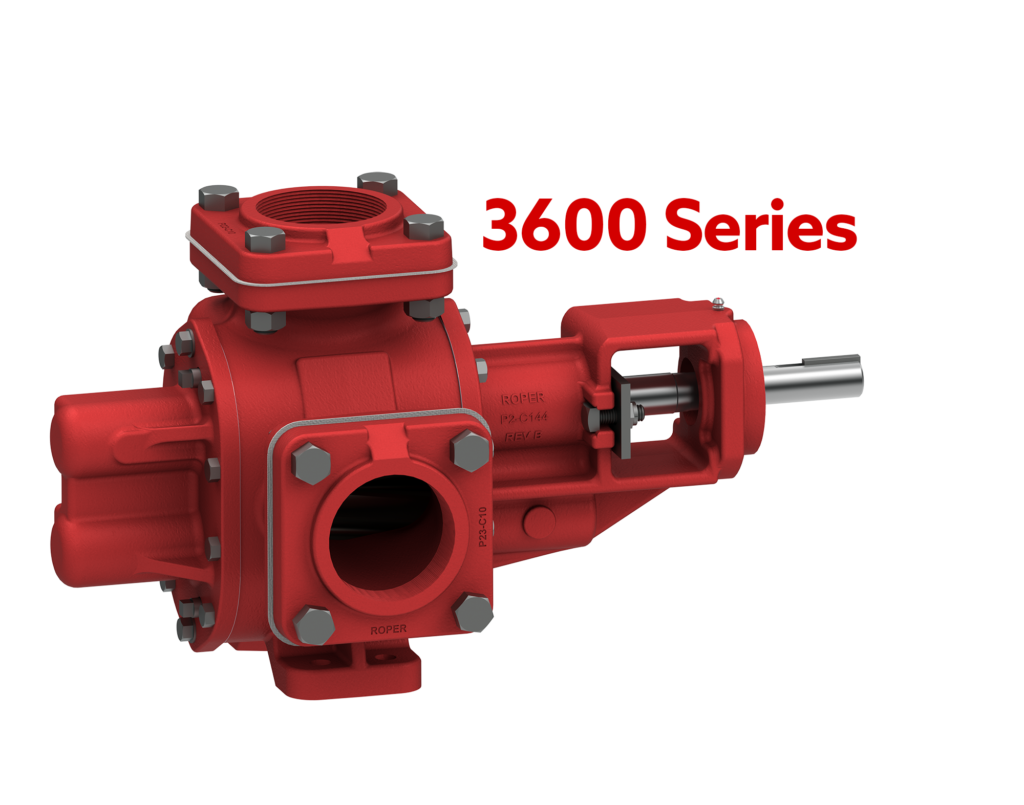
Chemical gear pumps have become indispensable tools for industries requiring precise fluid handling. Whether in chemical processing, pharmaceuticals, or manufacturing, their reliability and efficiency make them a preferred choice for transferring highly viscous or corrosive liquids. But what separates a high-performance chemical gear pump from the rest? Two key factors stand out above all others: flow accuracy and chemical resistance.
This blog will explore these defining characteristics, showcasing why they are critical for high-performance chemical gear pumps and how they influence industrial applications and longevity.
What Is a Chemical Gear Pump?
Before we explore its performance benchmarks, it helps to understand what a chemical gear pump is. Chemical gear pumps are specialized positive-displacement pumps designed to handle challenging, aggressive, and sometimes hazardous chemicals. Their functionality lies in the meshing of internal gears, which create pockets to move liquids with precision and consistency.
These pumps are widely used in industries such as:
- Chemical processing for transferring acids, solvents, and aggressive chemicals.
- Pharmaceuticals for precision dosing.
- Paint and coatings for handling viscous fluids like resins and adhesives.
- Food processing when sanitary handling of highly viscous liquids is required.
When dealing with substances as diverse as acids or thick polymers, ensuring precise flow and exceptional material resistance is not just advantageous but essential.
The Importance of Flow Accuracy
- Precision in Industrial Applications
Flow accuracy refers to a pump’s ability to deliver consistent and predictable flow rates, even under varying conditions like changes in viscosity, temperature, or pressure. For many chemical processes, precision is not a luxury; it’s a requirement for producing high-quality products.
For example, in pharmaceutical applications, where even the slightest deviation in liquid dosage can affect product efficacy, flow accuracy ensures that precise amounts are delivered without error.
- Improvements in Process Efficiency
Accurate flow minimizes errors in batch processing, reduces waste, and ensures operational efficiency. Consider industries working with costly chemicals or solvents. Over-pumping or under-pumping, even by a small margin, can lead to significant financial loss.
High-performance gear pumps are designed to maintain consistent delivery rates, regardless of fluctuations in operating parameters. This makes them invaluable for applications like metering systems or precise blending processes.
- Minimal Pulsation
One hallmark of exceptional flow accuracy is low pulsation. Unlike other pump types, gear pumps deliver a smooth, steady flow that doesn’t interrupt sensitive processes such as coating or continuous mixing. Pulsation-free flows translate to improved product consistency, especially for industries dealing with thin films or resins.
Chemical Resistance: The Second Pillar of High-Performance Gear Pumps
The ability to handle corrosive and abrasive materials without degradation is critical for pumps used in demanding chemical environments. Failures in chemical resistance can lead to leaks, downtime, and system failures that are both costly and hazardous.
- Material Longevity
High-performance chemical gear pumps are constructed with materials specifically selected for their compatibility with harsh chemicals. Common materials used include:
- Stainless steel for handling mild corrosive fluids and heat.
- PFA or PTFE coatings for a wide range of highly corrosive acids and solvents.
- Hastelloy and other exotic alloys for extreme applications requiring abrasion- and corrosion-resistant metals.
By resisting chemical wear, pumps can operate longer without maintenance, reducing downtimes.
- Broad Chemical Compatibility
Industries working with aggressive chemicals often require a single pump capable of handling a wide range of liquid types. Chemical-resistant materials expand a pump’s versatility, allowing it to safely transfer everything from concentrated alkalis to volatile hydrocarbons.
For instance, a paint and coating plant handling multiple fluids may require the transfer of resins, cleaning agents, and thinners. A poorly selected pump could corrode or degrade rapidly under such varied exposure, but one designed with superior chemical resistance offers lasting performance.
- Safety and Environmental Protection
A failure in chemical resistance doesn’t just compromise the pump; it poses significant safety risks. Leaks of hazardous solvents or corrosive fluids can lead to workplace accidents or even environmental contamination. A pump with robust chemical resistance safeguards both operators and the surrounding ecosystems.
Balancing Flow Accuracy and Chemical Resistance
While flow accuracy and chemical resistance are essential qualities on their own, their combined strength defines a truly high-performance chemical gear pump. The relationship between these attributes ensures that pumps can provide reliable, repeatable performance while standing up to their chemical challenges.
The Role of Advanced Engineering
Modern chemical gear pumps are the result of cutting-edge engineering that harmonizes mechanical precision with durable materials. Gear designs, clearances, and coatings are all optimized to meet the dual demands of accuracy and resistance, ensuring seamless operation across various temperatures, pressures, and viscosity ranges.
Real-World Applications
Consider the oil and gas industry, where sulfuric acid is commonly used in refining processes. A high-performance chemical gear pump must exhibit exceptional flow accuracy to effectively meter the acid while resisting its highly corrosive properties.
Similarly, in the pharmaceutical sector, viscous syrups and reactive solvents are transferred to production lines. Here, flow accuracy guarantees exact dosing, and chemical resistance ensures the pump withstands a wide range of solvents without contaminating the product.
Key Features to Look for in A High-Performance Chemical Gear Pump
When selecting a pump for your operations, consider these essential features to ensure optimal performance:
- Internal Materials are carefully selected for chemical resistance and durability.
- Advanced Sealing Mechanisms to prevent leaks and ensure system safety.
- Precision Engineering to optimize gear alignment for flow accuracy.
- Temperature and Pressure Resistance for compatibility with extreme operating conditions.
- Ease of Maintenance for reduced downtime and faster facility upkeep.
Investing in high-quality gear pumps designed with these features is cost-effective in the long run, minimizing replacement costs and ensuring steady, reliable performance.
Create Reliability with the Right Gear Pump
Flow accuracy and chemical resistance are the defining traits of high-performance chemical gear pumps. These pumps ensure that operations run smoothly, efficiently, and safely, even in the harshest environments. With precision delivery and robust material design, they meet the demands of modern industries that cannot afford inefficiencies or failures.
Whether you’re working in chemical processing, pharmaceuticals, or any high-stakes environment, selecting the right chemical gear pump ensures durability, consistent performance, and peace of mind.